EDUCATION
RESEARCH INTERESTS
Cavitation
Analysis of the fundamental mechanisms & modelling
2001
Institut National Polytechnique de Grenoble, France
PhD
Multiphase flows
Analysis of multi-component and/or multiphase flow configurations
Propulsion & Rotating Machinery
Study of the instabilities and performance variations generated by cavitation or non-nominal flow conditions
2008
University of Lille 1
Habilitation à Diriger des Recherches (HDR)
1997
Institut National Polytechnique de Grenoble
MS & Engineer Degree
RESEARCH TOPICS
The research activity of the group is mainly devoted to multiphase and multi-component flows. It focuses especially on cavitation, which is the vaporization of a liquid flow subjected to a local pressure drop. Cavitation is typically a multi-scale problem since it involves local transfers at interfaces, bubble interactions, all scales of turbulence, and large-scale organized instabilities. It is thus a complex and exciting phenomenon, which is harmful in large scale applications involving high speed flows, such as hydraulic machinery, injectors or naval propellers, but it is also very beneficial for chemical processes, medical and pharmaceutical applications, especially in configurations of micro and nano bubbles generated by acoustic waves or laser.
At large scale, i.e. for example in marine propellers and pumps, cavitation results in turbulent, compressible unsteady flows, in which the local proportion of gas varies between 0 and 100%. These properties – quite unusual in fluid mechanics - make the understanding of their structure and dynamics a challenging task. Cavitation induces detrimental effects such as performance decrease, instabilities and erosion after a long operating time, because of pressure waves due to the bubble collapses. In pumps, instabilities perturb the rotor equilibrium and lead to significant vibrations, which have been found responsible for the failure of the Japanese launcher H-II in 1999.
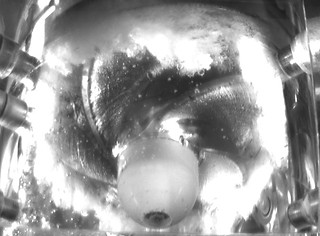



Rocket engine inducer (aspiration stage of the H2 pump) operating in cavitating conditions
Hydrogen inducer of Japanese launcher H-II (after the flight failure)
Radial efforts measured with an onboard balance in conditions of rotating cavitation
Conversely, at micro and nanoscale cavitation has a wide and increasing range of possible beneficial applications. Emerging fields of research are for example the treatment of cancerous cells in therapeutic research, ultrasound induced chemistry, and nanoscale emulsions encapsulating pharmaceutical agents that are water-insoluble. In these applications, both hydrodynamic and laser or ultrasound induced cavitation are used to activate small-scale mechanisms of pressure wave propagation, local hot spots or droplet tear off.
Cavitation induced oil/water emulsion
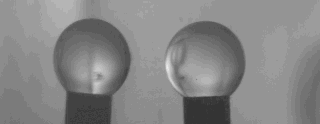
Cavitation in rotating machinery
Study of cavitation in pumps, and especially in space launcher turbopumps in collaboration with the CNES (French Space Agency) and SNECMA (manufacturer of the Ariane V engines) has been a permanent part of the work in the last 20 years.
The group has identified and analyzed various instability regimes caused by cavitation in the machinery, according to its geometry (for example the blade number), on the basis of full-scale water experiments. A special attention has been paid to the so-called “rotating cavitation” (non-symmetrical cavitation pattern on the blades, which rotates faster or slower than the machinery), which is among the most spectacular and dangerous for the rotor equilibrium. A numerical modeling of this regime has been successful performed and it was shown that the reattachment of the boundary layer on the blade suction side is responsible for the performance increase in case of rotating cavitation.

Simulation of rotating cavitation in a 4-blade cascade derived from a 3D turbopump inducer
The current investigations aim to identify and eventually control the mechanisms that initiate the instabilities due to cavitation. For that purpose, the internal flows in turbomachinery will be investigated by the various experimental means that have been developed in the recent years, as explained hereafter.



Fast start-up of a pump: (a) head drop evolution (red),
(b) evolution of the vapor volume inside the impeller.
The group has also simulated fast start-ups of space turbomachinery (from 0 up to 3000 rpm in 3 rotations) on a test facility, in order to characterize the transient cavitation and its effects on the performance. Original measurements by X-ray imaging have provided the time evolution of the vapor within the impeller during the start-up. This work has resulted in a functional modelling of the pump including the effects of cavitation, which was shown to be efficient for various types of start-ups
Physical mechanisms of unsteady hydrodynamic cavitation

The objective is to characterize the physical mechanisms that control cavitating flows, by original experimental means, as standard one are usually useless. A special attention has been paid to the morphology and dynamics of sheet cavities generated on 2D foil sections and Venturi type sections. Other issues such as the influence of the wall roughness have also been considered.
A better understanding of the morphology of cavitation has been obtained by the means of X-ray imaging and endoscopic visualizations. Simultaneous fast measurements of the void fraction and velocities in both phases have also been conducted by joint development of i) X-ray imaging, ii) Particle Image Velocimetry (PIV) with fluorescent particles. It has enabled to characterize, for the first time, the dynamics of each phase, and thus determine the slip velocities, which were neglected in all models, but were found to be locally of about 50% of the liquid velocity in average

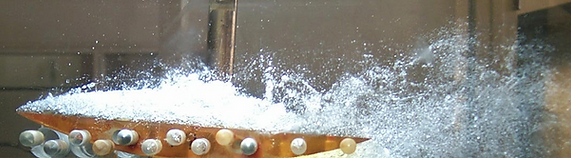


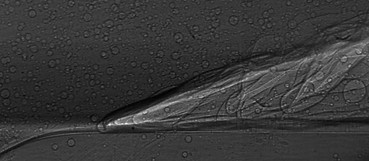
Sheet cavity on a 2D foil section
The group has also performed successful measurement of the speed of sound within a cavitation medium by acoustic means, which enabled to validate the theoretical models of wave propagation within two-phase flows (Wallis, Jakobsen) that were applied since the 60s. These measurements will be now repeated at various temperatures, in order to evaluate the stiffness of the mixture and thus to obtain the amount of non condensable gas trapped in the vapor bubbles. This parameter is of primary importance for modelling and understanding of the small scale properties of cavitation.
These various novel data, associated with the numerical work presented in the next section, will converge in the next five years to a ground-breaking modelling of cavitation, by characterizing the mechanisms that control the processes of phase change, momentum and heat exchanges between the two phases, and turbulent interactions.
X-ray imaging of a sheet cavity (see the bubble interfaces and the hollow glass sphere tracers for PIV)
Morphology of a sheet cavity
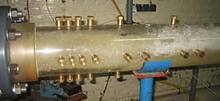

(a) Laser illumination of the sheet cavity, (b) non dimensional slip velocity
Speed of sound according to the void fraction
Modelling of cavitating flows
The research group has addressed a large variety of issues, whose general framework is the coupling of the Navier-Stokes equations with a so-called “cavitation model”, which manages the inception of the vapor phase and its interaction with the liquid.
An in-depth theoretical study of the governing equations for the cavitating flows has been conducted. The notion of “two-phase flow particle” has been proposed by analogy with the “fluid particle”, and it has been shown that the well known “single fluid” (or homogeneous) and “2 fluids” approaches, initially proposed by Ishii in 1975, are basically equivalent.
Turbulence modelling in cavitating conditions has been extensively studied: a modification of the RANS k-e model, which lowers the turbulent viscosity in the two-phase areas, has been successfully applied in the early 2000s to reproduce some self sustained instabilities due to cavitation. This modified version of the model is now widely applied in commercial solvers, to simulate the cavitation instabilities. A theoretical analysis has shown a posteriori that the proposed modification was equivalent to include the compressibility effects in the turbulence modelling. It has been demonstrated recently - about 20 years after it has been proposed, that it leads to a shear stress in close agreement with the data derived from X-ray imaging !
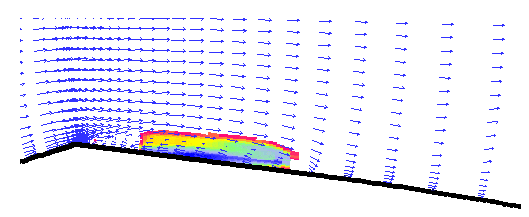
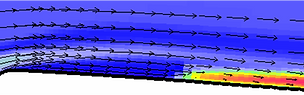

URANS simulation of unsteady cloud cavitation
Turbulent Viscosity downstream from the sheet cavity (a) standard k-e model, (b) modified model


Modification of the k-e model proposed to reproduce the instabilities associated with cavitation
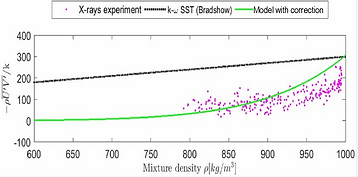
Comparison btween the predicted and measured shear stress at the red square location

A numerical model for the prediction of erosion has been also developed through a coupling between CFD simulations, including the liquid compressibility to reproduce the propagation of the pressure waves towards the solid surface, and an erosion model, which calculates the subsequent impacts.
Measured and predicted damage on the surface
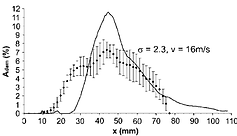
The research is now focused on a first direct turbulence simulation (DNS), in order to fix the poor prediction of the cavitation/turbulence interactions with RANS models. The next step will be to extract from all available data empirical properties for the physical mechanisms. i.e. obtaining laws that fit the experimental or numerical results, and finally derive equations for the flow. Implementation of the model into a solver will enable predictive CFD simulations in complex flows of industrial interest, especially for space and marine applications. Collaboration has been initiated on this topic with Prof. H. Xiao, from the OAE department of VaTech, to quantify model form uncertainties in the RANS equations used to model cavitation.
Small scale mechanisms
The exploration of these topics has been initiated in the very last years, in the scope of active efforts to include in the Group activity emerging applications of cavitation, associated with hot industrial concerns.
Cavitation erosion has been investigated by using an aluminium foil as sensor, while cavitation was generated by means of ultrasounds. Attention has been focused on the process of single pit and pit cluster formation. The connection between the foil deformation and the collapse of the clouds of vapor bubbles has been demonstrated. Such knowledge regarding the formation of the pit that eventually leads to the mass loss is of primary importance for the future development of predictive physical models of cavitation erosion in pumps and naval propellers.

Analysis of the thermal effects in the liquid by IR thermography during the growth and collapse of a vapor bubble
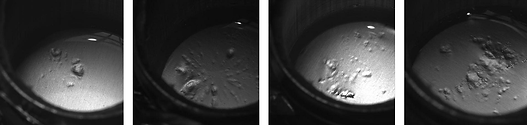
Cavitation erosion on aluminium foils after 10s exposure
Cold wire for local high frequency temperature measurement inside a cavitation bubble during growth and collapse

Thermal effects associated with phase changes are currently investigated, as the characterization of this phenomenon is crucial for the design of the rocket engine turbopumps, and more generally all applications of cryogenic liquids, which emerge currently. IR thermography has already enabled to quantify, for the first time, the heat exchanges associated with the growth and collapse of a single vapor bubble. This work will be extended in the future to water temperature up to 250°F, to investigate higher magnitudes of thermal effects (cooling during vaporization increases drastically in hot water). Temperature will be measured for example with cold wire thermometers of micrometric diameter, to reduce the flow perturbation and minimize the time of response.
Study of cavitation induced nano and micro oil/water emulsions has been initiated recently. Attention is focused on the morphology of the emulsion and its stability in time. This new emerging topic, which has an increasing number of applications in pharmaceutical industry and industrial processes, aims to extend my activities to nanotechnology applications based on ultrasonic and laser induced cavitation. Application of imaging techniques developed in the last years (X-ray, nano and micro thermometers, IR thermography) will enable to characterize the two-components medium according to various parameters of interest.
Environmental flows
Investigation of oil/water/air mixture behaviors associated with oil spilled in ocean or lakes is currently conducted in the scope of a collaboration with Prof. Katz, from Johns Hopkins Univ. Direct numerical simulations are perform in the research group in two particular configurations: a rain drop falling on a deep pool of water on which a thin layer of oil is floating, and an oil jet rising in water while submitted to a cross flow. In the first case, attention is focused on the effect of the oil layer thickness on aerosol formation and oil spill dispersal, while in the second case, the effect of chemical dispersant on the jet atomization and final size of oil droplet is investigated.


Experiments and simulations of oil jet in water cross flow (Experiments performed at JHU)
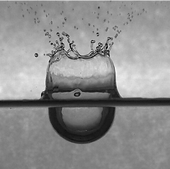
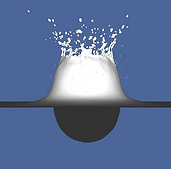
Simulation of water drop in a pool of water with an oil layer at the surface (Experiments performed at JHU)
More generally, oil spill introduces a broad range of problems related to environmental concerns, such as oil flows, mud flows and ground flows, for which the numerical and experimental techniques and skills developed for cavitation may be of great interest, as they involve multi-component and multiscale mechanisms.